Welcome to I-Form: Advancing Manufacturing Through Research
About
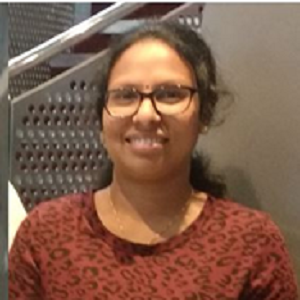
Dr
Sithara Sreenilayam
Funded Investigator
DCU
Dr. Sreenilayam is Assistant Professor in the School of Mechanical and Manufacturing Engineering, Dublin City University since June 2023. Dr Sreenilayam is a Principal Investigator in the Advanced Processing Technology Research Centre, Dublin City University and Funded Investigator in the I-Form, The SFI Research Centre for Advanced Manufacturing. She received M.Sc. in physics from Mahatma Gandhi University, India, and Ph.D. in Soft Matter Physics from the Technological University Dublin (TUD), Ireland. Her Ph.D. focused on fundamental soft matter physics underpinning the next generation of novel functional materials. Dr Sreenilayam has extensive research experience in Soft Matter Science, Fibre Optics, Laser systems, Photovoltaics, Advanced Manufacturing, Nanomaterials, and flexible printed electronics.
Research Interests (Lay Summary)
Dr Sreenilayam has extensive research experience in Soft Matter Science, Fibre Optics, Laser systems Advanced Manufacturing and Nanomaterials. Her research interest has focused on the fundamental soft matter physics underpinning the next generation of novel functional materials. The main focus is to combine the significant features of soft matter self-assembly with nanoscience and additive manufacturing; to design and invent functional materials and exploit them for fast electro-optic device, Photovoltaic and biomedical applications.
Dr Sreenilayam joined I-Form in January 2020 and since then she has been working in a project that aims to perform transformative research on advanced photovoltaic solar cell technology to extend the state of the art in three areas: advanced manufacturing processes; materials for high performance, low cost photovoltaic technology; and using photovoltaics to power IoT devices from indoor light sources. The project may provide an improved process that will increase the cost effectiveness and sustainability of solar cell production and remove a hard limit on the growth of solar energy.
Technical Summary
Present silicon solar cells utilize silver screen-printing to form the front electrode, and the silver paste is the second most expensive material in the cells. Copper is an order of magnitude cheaper than silver. The narrower, higher conductivity plated copper electrodes can increase solar cell efficiency by up to 10% compared to screen-printed silver electrodes. However, present attempts to manufacture cells with copper plating have been stymied by poor reproducibility caused by seed layers that are not robust or are poorly adhered. So the aim of the project is the development of an additive-manufactured metal seed layer for plating of Cu electrodes and employ it to make reliable solar cells with low resistive and shadowing losses. For plating copper electrodes, inkjet printable copper nanoparticle based inks generate via pulsed laser ablation in liquids (PLAL), a technique developed in I-Form. The inkjet printable inks and process parameters for inkjet printing will be optimised, based on post-process characterisation of the seed layers, for composition, line-width, conductivity, continuity, print-speed, and reduced material usage. The developed seed layer annealing by laser will be carried out to improve conductivity and continuity. If the assessment on manufacturability indicates the suitability of this technique, the project may provide an advanced process that will increase the sustainability and cost effectiveness of PV solar cell production and overcome the limit on the solar energy growth.