Researcher Spotlight: Advancing Additive Manufacturing Research at I-Form
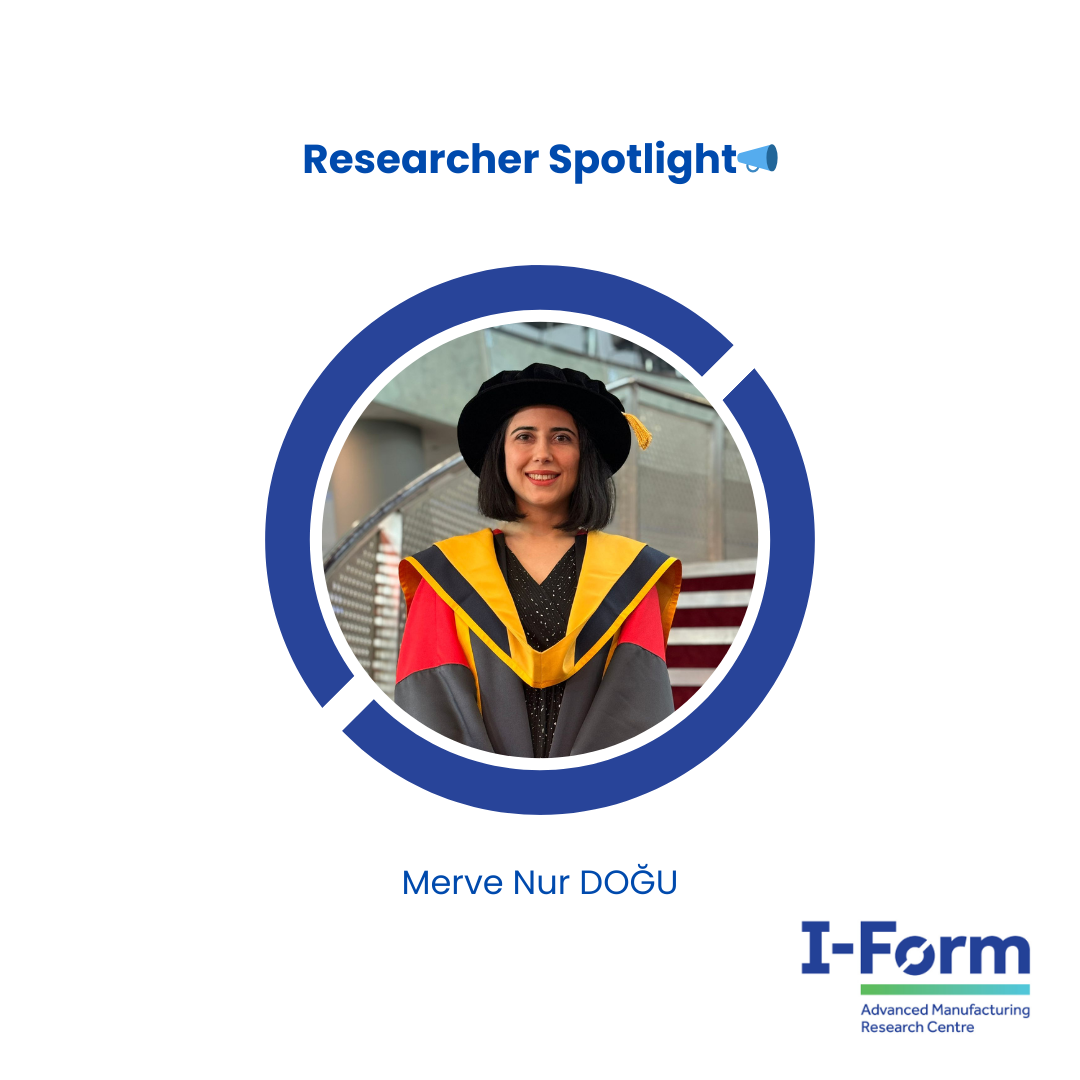
The field of additive manufacturing (AM) continues to push the boundaries of materials science and engineering, especially in the aerospace industry, where strong, durable, and heat-resistant components are critical. At the heart of this research is Dr Merve Nur Doğu, a postdoctoral researcher at I-Form, Research Ireland Centre for Advanced Manufacturing. With her expertise in mechanical and manufacturing engineering, Dr Doğu is working on pioneering projects that aim to deepen our understanding of powder bed fusion-laser beam (PBF-LB) techniques, improve process monitoring, and ultimately enhance quality assurance in AM.
Bridging Additive Manufacturing and Real-World Applications
Dr Doğu is involved in two major research projects at I-Form. The first project, Digital Laser Production: Digital Twins of Laser Processing for Multi-Capability Manufacturing of Complex Components, explores the use of digital twins in laser processing. This technology creates virtual replicas of laser-manufactured components, allowing for real-time simulations, testing, and improvements that directly influence the manufacturing process. The goal is to develop a more adaptable manufacturing framework for creating complex components across a variety of industries, thereby pushing AM closer to mainstream adoption.
Her second project, Certification and Development of an Additive Manufacturing Production Knowledge Base and Models for Prediction of Microstructure, is conducted in partnership with Ansys Inc., a leading engineering simulation software company. This work focuses on developing a robust knowledge base and predictive models that will help AM practitioners forecast microstructural changes in materials, an essential step for certifying AM processes and ensuring consistent, high-quality outputs.
Foundation in Materials Science
Dr Doğu’s academic journey began in Turkey, where she earned her BSc in Materials Science and Engineering at Çankaya University, followed by an MSc in Metallurgical and Materials Engineering from Middle East Technical University (METU). During her master's studies, she delved into the thermo-hydrogen processing of the Ti6Al4V alloy, a widely used material in aerospace, produced by Electron Beam Melting (EBM).
This year Dr Doğu completed her PhD at Dublin City University, where she focused on the additive manufacturing of the nickel-based superalloy IN939 using PBF-LB technology. Her research offers crucial insights into the behavior and properties of this high-performance alloy, which is used in gas turbine engines and other demanding aerospace applications.
Pioneering Process Monitoring for Enhanced Quality Assurance
A significant part of her research focusses on understanding the intricate relationships between PBF-LB process parameters, metal powder characteristics, and post-processing treatments, and their cumulative impact on material microstructure and mechanical properties. Her studies cover various factors, including particle size, laser power, spot size, build layer thickness, pre-heating temperature, and scanning speed.
Her expertise is particularly relevant to industries requiring components that can withstand extreme conditions, like aerospace. By meticulously analysing how initial material characteristics and AM parameters affect superalloys such as IN718 and IN939, she aims to enable manufacturers to produce stronger, more resilient, and defect-free components for use in high-stakes applications like gas turbines and rocket systems.
One of the central challenges in additive manufacturing is ensuring consistent quality in complex, high-value components. To address this, her research also investigates the role of process monitoring systems as a method of quality assurance. These systems enable near-real-time detection of defects, especially in the porous structures often required in lightweight aerospace parts. By integrating advanced monitoring technologies into AM, she is advancing a framework that could allow manufacturers to catch defects early in the production process, reducing waste and improving reliability.
Shaping the Future of Additive Manufacturing and Aerospace Applications
Merve’s work at I-Form is not only shaping the future of AM but also addressing the needs of industries that rely on complex, high-performance materials. By exploring digital twins, enhancing process parameters, and advancing quality assurance methods, her research has the potential to inform the standards of additive manufacturing in aerospace and beyond. Her research has the potential to pave the way for more reliable, safer, and efficient aerospace technologies. Her contributions at I-Form underscore the importance of collaborative research efforts and illustrate how advanced manufacturing research can address real-world industrial challenges. With researchers like Merve, the field of additive manufacturing is poised to make even more remarkable strides in the near future.